manual handling for disability support workers
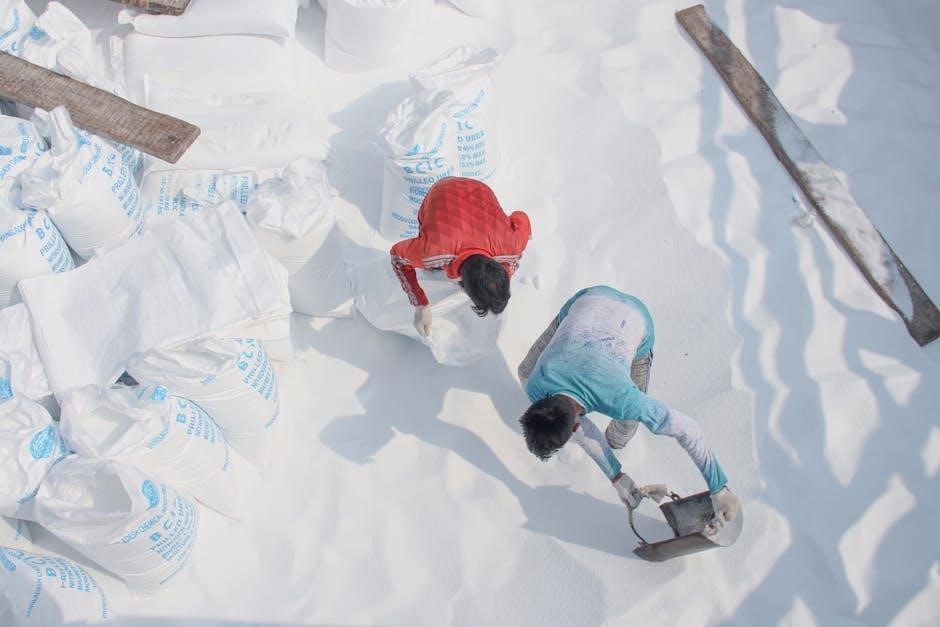
Manual handling in disability support involves physical effort to move or assist individuals. This guide emphasizes safety for both the support worker and the person with a disability. Proper training is crucial, and this training provides essential skills and techniques for safe support practices;
Understanding Manual Handling Risks in Disability Support
Disability support work carries significant manual handling risks. Improper techniques can lead to musculoskeletal disorders for caregivers. Workplace injuries are a serious issue, accounting for a large percentage of claims. Reducing these risks requires careful assessment, planning, and training. Prioritizing safety is paramount.
Common Injuries and Their Causes
Manual handling in disability support can lead to various injuries, primarily musculoskeletal disorders. These often result from repetitive tasks, awkward postures, and excessive force. Acute back injuries are common, frequently stemming from improper lifting techniques or handling loads beyond one’s capacity. These injuries can become acute, leading to disabling conditions.
Other common injuries include strains, sprains, and hernias, often caused by incorrect posture, twisting motions, or failing to use assistive devices. The cumulative effect of these actions can lead to chronic pain and long-term disability for support workers. Risk factors include inadequate training, poor physical fitness, and environmental hazards.
Understanding these risks and their causes is vital for implementing preventative measures. Proper assessment of manual tasks, coupled with appropriate training and the use of assistive equipment, can significantly reduce the incidence of these injuries, ensuring a safer working environment for disability support staff.
Legal and Ethical Considerations
Manual handling in disability support is governed by legal and ethical standards to protect both workers and individuals receiving care. Workplace health and safety laws mandate employers to minimize risks associated with manual handling. Providers must undertake risk assessments and implement safety protocols to comply with these regulations.
Ethically, support workers have a duty of care to ensure the safety and well-being of the individuals they assist; This includes using safe handling techniques and respecting the person’s dignity and autonomy. Failing to do so can result in legal repercussions and ethical breaches.
Furthermore, informed consent is crucial. Support workers should explain handling procedures to the individual, ensuring they understand and agree to the process. Confidentiality regarding a person’s health and abilities must also be maintained. Balancing the need for safe manual handling with the individual’s rights and preferences requires careful consideration and adherence to ethical guidelines.
Principles of Safe Manual Handling
Safe manual handling involves assessing tasks, using proper techniques, and employing assistive devices. Good posture and habits are essential, along with regular exercise. Planning, communication, and tailored approaches minimize strain and reduce injury risks for disability support workers.
Assessing the Task and the Environment
Before undertaking any manual handling task, a comprehensive assessment is crucial. This involves evaluating the individual’s needs, mobility level, and any specific conditions that may affect the handling process. Consider the weight and stability of the person, as well as any equipment involved, such as wheelchairs or walking aids.
The environment also plays a significant role in safe manual handling. Ensure the workspace is clear of obstacles, well-lit, and has adequate space for movement. Check for potential hazards like slippery floors or uneven surfaces. Hand and grab rails should be assessed for their condition and suitability.
Evaluate if assistive devices are available and in good working order. This includes electric stand chairs, modified chairs, leg lifters, and transfer belts. Proper risk assessment and management are vital to minimize risks associated with manual handling, adhering to work, health, and safety requirements.
Effective communication with the individual is paramount to understand their preferences and any limitations they may have. This collaborative approach ensures a safer and more comfortable experience for everyone involved.
Proper Lifting and Carrying Techniques
Employing correct lifting and carrying techniques is paramount to prevent injuries. Stand close to the person being supported, maintaining a wide base of support for stability. Bend your knees, keeping your back straight to engage your leg muscles, rather than straining your back.
Keep the person close to your body to minimize the load on your spine. Avoid twisting or jerking movements while lifting or carrying. Instead, pivot your feet to change direction, maintaining a smooth and controlled motion.
When supporting someone to stand, ensure a firm grip and communicate clearly about the steps involved. Encourage the individual to participate actively, using their own strength whenever possible. If the load is too heavy or awkward, seek assistance or use appropriate assistive equipment.
Regular exercise and maintaining good posture are essential for preventing manual handling injuries. Adopt good habits and use safe practices consistently. Proper lifting and carrying techniques protect workers and ensure the comfort and safety of the individuals they support.
Using Assistive Devices and Equipment
Assistive devices and equipment are crucial in reducing the risk of manual handling injuries. These tools aid in safely moving individuals with varying levels of mobility. Equipment includes hand and grab rails, electric stand chairs, modified chairs, leg lifters, and bed sticks.
Walking aids, such as frames or sticks, provide support and stability. Transfer belts assist in safe transfers, while pallet jacks and trolleys help move heavier objects. Ensure equipment is in good working condition before use, checking for any damage or wear.
Proper training is essential for operating assistive devices correctly. Understand the device’s limitations and follow manufacturer instructions. When selecting equipment, consider the individual’s needs and the specific task.
Regularly maintain and inspect equipment to ensure its safety and effectiveness. Report any issues or malfunctions immediately. By utilizing assistive devices and equipment, disability support workers can minimize physical strain and create a safer environment for both themselves and the individuals they support.
Practical Manual Handling Techniques for Disability Support
This section covers essential techniques for disability support, including assisting with transfers, supporting mobility, and providing personal care. These techniques aim to reduce the risk of injury while ensuring the comfort and dignity of the individual.
Assisting with Transfers
Assisting with transfers is a critical aspect of manual handling for disability support workers. It involves safely moving an individual from one surface to another, such as from a bed to a wheelchair. Proper techniques are essential to minimize the risk of injury for both the support worker and the person being assisted.
Before initiating any transfer, a thorough assessment of the individual’s abilities and limitations is necessary. This includes evaluating their strength, balance, and cognitive function. The environment should also be assessed to ensure it is free from obstacles and provides adequate space for the transfer.
Effective communication is paramount throughout the transfer process. Clearly explain the steps involved to the individual and encourage their active participation to the best of their ability. Utilize assistive devices, such as transfer belts or boards, whenever appropriate to reduce strain and enhance safety.
Maintaining proper body mechanics is crucial for preventing injuries. Keep your back straight, bend your knees, and use your leg muscles to lift and support the individual. Avoid twisting or jerking movements, and always maintain a firm grip. Remember to work as a team when possible, especially for individuals who require significant assistance.
Supporting Mobility
Supporting mobility is a key responsibility of disability support workers, requiring careful manual handling techniques. This involves assisting individuals with movement, whether it’s walking, standing, or repositioning. The goal is to promote independence and safety while minimizing the risk of injury.
Before assisting with mobility, assess the individual’s needs and capabilities. Consider their balance, strength, and any physical limitations. Choose appropriate assistive devices, such as walkers, canes, or wheelchairs, based on their needs and preferences. Ensure these devices are in good working condition and properly fitted.
When assisting with walking, provide support at the individual’s side or slightly behind them, using a gait belt if necessary. Encourage them to maintain good posture and take slow, steady steps. Be mindful of potential hazards in the environment, such as uneven surfaces or obstacles.
For individuals who use wheelchairs, ensure the brakes are locked before assisting with transfers or repositioning. When pushing a wheelchair, maintain a comfortable posture and avoid sudden stops or turns; Communicate clearly with the individual to ensure their comfort and safety throughout the process.
Personal Care Assistance
Providing personal care assistance to individuals with disabilities often involves manual handling tasks. This can include assisting with dressing, showering, toileting, and other hygiene-related activities. It’s crucial to approach these tasks with sensitivity, respect, and a focus on maintaining the individual’s dignity.
Before providing assistance, communicate clearly with the individual about what you’ll be doing and how they can participate. Encourage them to do as much as they are able to, promoting their independence and self-esteem. Always respect their preferences and choices.
When assisting with dressing, ensure the individual is in a comfortable and safe position. Use proper body mechanics to avoid strain, such as bending your knees and keeping your back straight. Consider using adaptive clothing or assistive devices to make the process easier.
For showering or bathing, ensure the bathroom is safe and accessible. Use non-slip mats and grab bars to prevent falls. Assist with washing and drying as needed, respecting the individual’s privacy and modesty. When assisting with toileting, provide support and assistance as needed, while maintaining their dignity and independence.
Training and Competency
Comprehensive manual handling training is paramount for disability support workers. It equips them with the knowledge and skills to safely assist individuals, minimizing the risk of injuries to both the worker and the person they support. Training should cover risk assessment, proper lifting techniques, and the use of assistive devices.
The training programs should address specific needs within the disability sector. They should include practical, hands-on sessions where workers can practice techniques under supervision. Regular refresher courses are essential to reinforce skills and update knowledge on best practices.
Competency assessments should be conducted to ensure workers can safely and effectively apply learned techniques. These assessments may involve observing workers during simulated or real-life scenarios. Ongoing professional development is vital to maintain competency and adapt to evolving client needs and industry standards.
Employers have a responsibility to provide adequate training and resources. This includes ensuring workers have access to appropriate equipment and support. A commitment to training and competency creates a safer work environment and improves the quality of care provided.
Maintaining a Safe Work Environment
A safe work environment is crucial for disability support workers to prevent manual handling injuries. Regular risk assessments are essential to identify potential hazards and implement control measures. This includes evaluating the physical environment, tasks performed, and individual client needs.
Clear communication protocols should be established to ensure workers can report concerns and receive support. Accessible and well-maintained equipment, such as hoists and transfer aids, is vital for safe manual handling practices. Workspaces should be organized to minimize clutter and obstacles, allowing for smooth movement.
Employers should promote a culture of safety where workers feel empowered to prioritize their well-being. This includes encouraging the use of proper techniques and providing adequate rest breaks. Regular equipment checks and maintenance are necessary to ensure optimal functionality.
Policies and procedures related to manual handling should be readily available and consistently enforced. Collaboration between workers, supervisors, and clients is key to identifying and addressing safety concerns. A proactive approach to safety helps prevent injuries and fosters a supportive work environment.